Plastic granules are the building blocks of countless everyday items, forming the foundation of the modern plastic manufacturing industry. These tiny, bead-like pieces of processed plastic are used as raw materials in producing everything from household goods to industrial components. Their versatility, cost-effectiveness, and adaptability to various manufacturing processes make them indispensable across industries.
Understanding plastic granules is crucial not only for businesses but also for promoting sustainable practices in the global effort to reduce plastic waste. For industries, plastic granules streamline production, enabling cost-efficient and scalable solutions. From packaging and construction to automotive and electronics, their applications span a wide range of sectors. Additionally, with the growing emphasis on environmental sustainability, recycled plastic granules are emerging as a key player in reducing waste and conserving resources.
By delving into what plastic granules are and their role in both manufacturing and recycling, we can better appreciate their significance in shaping a more sustainable and efficient future. This guide will help you understand the basics of plastic granules, their types, and why they matter for industries and the environment alike.
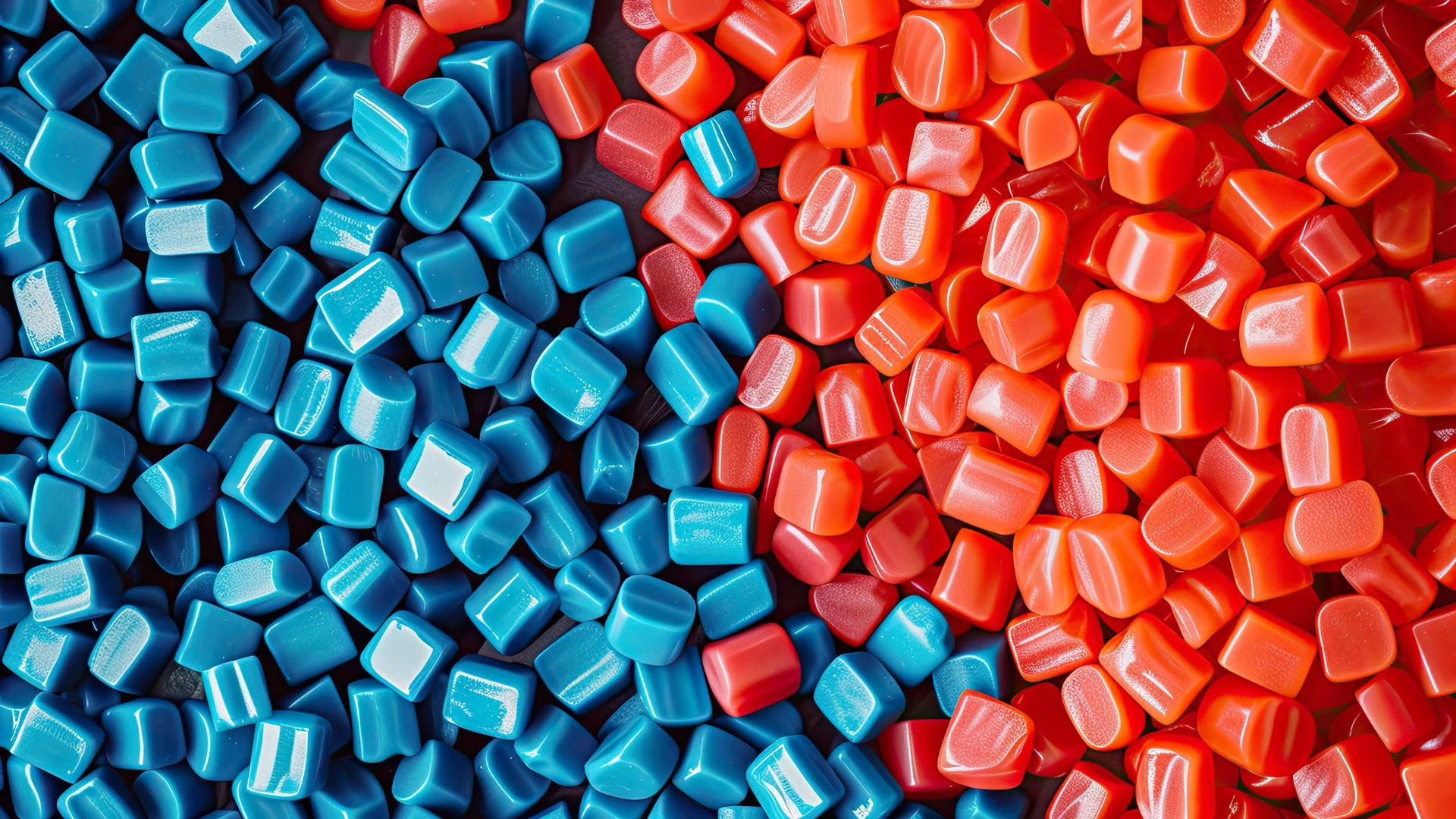
What Are Plastic Granules?
Plastic granules are small, pellet-like pieces of plastic that serve as the primary raw material for manufacturing a wide variety of plastic products. They are created through processes such as polymerization, extrusion, and pelletizing, resulting in uniform particles that can be easily melted and molded into desired shapes. These granules come in various forms, such as virgin plastic granules, recycled plastic granules, and specialty granules designed for specific applications.
The role of plastic granules in manufacturing is pivotal. They offer a standardized and efficient way to produce plastic products in bulk, ensuring consistency in quality and performance. Industries across the globe rely on these granules for making items like packaging materials, household goods, automotive components, and even medical devices. The uniform size and texture of plastic granules make them compatible with different manufacturing methods, including injection molding, extrusion, and blow molding.
Plastic granules also play a critical role in promoting sustainability within the industry. By recycling plastic waste into new granules, manufacturers can significantly reduce the environmental impact of their operations. This shift not only helps in conserving resources but also aligns with the increasing demand for eco-friendly products.
Types of Plastic Granules
Plastic granules come in various forms, each tailored to meet specific industrial needs. Understanding the differences between these types can help businesses choose the most suitable option for their products and processes. Here are the main types of plastic granules:
1. Virgin Plastic Granules
Virgin plastic granules are made from raw, unprocessed petrochemical materials. These granules are free from impurities and exhibit consistent quality, making them ideal for high-precision applications.
Characteristics:
- Uniform composition and high purity.
- Excellent mechanical strength and durability.
- Available in various types such as LDPE granules, HDPE granules, and PP granules.
Uses: Virgin plastic granules are commonly used in industries where stringent quality standards are required, such as food packaging, medical devices, and automotive components. Their superior properties ensure reliable performance and long-lasting products.
2. Recycled Plastic Granules
Recycled plastic granules are produced from discarded plastic materials, which are collected, processed, and transformed into reusable granules. These granules are a vital component of the circular economy, helping reduce plastic waste and conserving natural resources.
Importance in Sustainability:
- Minimizes the environmental impact by diverting plastic waste from landfills.
- Reduces the demand for virgin plastics, conserving fossil fuels.
- Offers a cost-effective alternative for manufacturers without compromising usability.
Uses: Recycled granules are widely used in industries like construction, agriculture, and packaging, where the focus is on cost-efficiency and eco-friendliness rather than premium quality.
3. Specialty Plastic Granules
Specialty plastic granules are engineered to meet specific application requirements, such as high strength, chemical resistance, or heat tolerance. These granules are often tailored by adding additives or combining different polymer types.
For Specific Applications:
- High-strength granules for automotive and aerospace components.
- Heat-resistant granules for electrical appliances and industrial equipment.
- UV-stabilized granules for outdoor applications like garden furniture and pipes.
Uses: Specialty granules are used in advanced manufacturing processes that require customized material properties. Their adaptability makes them a popular choice for niche markets and innovative applications.
Each type of plastic granule serves a unique purpose, catering to diverse industrial needs while contributing to sustainability efforts. Choosing the right type depends on factors like product requirements, cost considerations, and environmental goals.
How Are Plastic Granules Made?
The production of plastic granules involves a series of well-defined steps designed to transform raw materials into uniform, high-quality granules suitable for manufacturing. Let’s explore the process in detail:
1. Raw Material Processing
The journey of plastic granules begins with the selection and preparation of raw materials. These materials can either be petrochemical-based for virgin granules or recycled plastic waste for eco-friendly granules.
Steps Involved:
- Virgin Granules: Petrochemical compounds, such as ethylene or propylene, are extracted and refined to produce base polymers like polyethylene or polypropylene.
- Recycled Granules: Discarded plastic waste is collected, sorted, and cleaned to remove contaminants like labels, adhesives, and dirt.
- The processed raw materials are then broken down into smaller pieces, ensuring consistency for the next stage.
2. Extrusion and Pelletizing Process
Once the raw materials are ready, they undergo extrusion and pelletizing, which are central to granule production. This process shapes the plastic into its final granulated form.
Extrusion Process:
- The raw material is melted in a heated extruder, where it is mixed and homogenized into a uniform molten plastic.
- Additives, such as colorants, stabilizers, or performance enhancers, are often introduced during this stage to modify the granules’ properties.
Pelletizing Process:
- The molten plastic is forced through a die, creating continuous strands of plastic.
- These strands are cooled using water or air to solidify them.
- Once solidified, the strands are chopped into small, uniform granules.
3. Key Steps in the Production Process
The production process is optimized to ensure efficiency, quality, and uniformity. The following steps are crucial:
- Material Inspection: Ensuring the raw material is free from impurities.
- Melting and Mixing: Achieving a uniform consistency for optimal granule performance.
- Strand Formation: Using precision dies to create consistent strands.
- Granule Cutting: Chopping the strands into uniform sizes to produce pellets.
- Cooling and Drying: Removing moisture to prevent quality degradation.
- Quality Control: Testing granules for size, shape, and performance parameters.
By following these steps, manufacturers produce granules like LDPE Granules, HDPE Granules, and PP Granules that meet industry standards. The process can also be tailored for specific applications, ensuring that the final product aligns with the intended use.
Applications of Plastic Granules
Plastic granules play a pivotal role across a wide array of industries due to their versatility, cost-efficiency, and adaptability to various manufacturing processes. Their widespread use can be attributed to their ability to meet diverse industrial demands while offering consistent quality. Let’s delve into the industries and products that rely on plastic granules:
1. Common Industries Using Plastic Granules
- Packaging Industry
The packaging industry is one of the largest consumers of plastic granules, especially LDPE Granules and HDPE Granules.- Used for making flexible packaging materials like plastic bags, wraps, and films.
- Essential for rigid packaging like bottles, containers, and caps.
- Construction Industry
Plastic granules are extensively used in construction materials due to their durability and resistance to environmental factors.- Applications include pipes, fittings, insulation materials, and roofing sheets.
- Automotive Industry
The automotive sector relies on granules for manufacturing lightweight, durable, and heat-resistant components.- Used in dashboards, bumpers, and interior trims.
- Specialty granules ensure high performance in demanding conditions.
- Consumer Goods Industry
Everyday items like household products, kitchenware, and toys are made using plastic granules.- PP Granules are particularly popular for producing durable goods like furniture and storage solutions.
- Agriculture Industry
In agriculture, granules are used for making essential products such as irrigation pipes, greenhouse films, and seed trays.
2. Examples of End Products Made from Plastic Granules
Plastic granules are transformed into countless products we use daily. Here are some examples:
- LDPE Granules: Flexible plastic bags, shrink wraps, and agricultural films.
- HDPE Granules: Milk bottles, detergent containers, and water pipes.
- PP Granules: Food containers, automotive parts, and textile fibers.
- Specialty granules are used to produce advanced materials like heat-resistant containers, UV-stabilized outdoor furniture, and medical-grade equipment.
The wide-ranging applications of plastic granules showcase their indispensability in modern manufacturing. Their ability to adapt to various requirements makes them a cornerstone of industrial and consumer products.
Why Are Plastic Granules Important?
Plastic granules are vital to the modern manufacturing industry due to their versatility, cost efficiency, and role in sustainability. Their adaptable nature allows them to be molded into a wide range of products, from packaging and automotive parts to household goods and construction materials. This versatility ensures they meet the diverse needs of various industries.
Granules contribute significantly to cost efficiency and scalability in production. Their uniform size and composition streamline manufacturing processes, reducing waste and production costs while enabling large-scale output without compromising quality.
Moreover, plastic granules play a crucial role in sustainable recycling practices. Recycled granules help reduce plastic waste, conserve resources, and lower the environmental impact of manufacturing. By integrating recycled materials, businesses align with eco-friendly practices and the growing demand for sustainable solutions.
Benefits of Using Recycled Plastic Granules
Recycled plastic granules offer a wide range of advantages, making them a preferred choice for industries seeking cost-effective and sustainable solutions. Here are the key benefits:
1. Environmental Impact and Waste Reduction
Recycled plastic granules significantly reduce the amount of plastic waste that ends up in landfills and oceans. By repurposing discarded plastics into reusable granules, manufacturers contribute to:
- Lower greenhouse gas emissions by reducing the need for virgin plastic production.
- Conservation of natural resources, such as crude oil and natural gas, which are primary raw materials for virgin plastics.
- A cleaner environment, promoting a circular economy and sustainable development.
2. Cost-Effectiveness Compared to Virgin Granules
Recycled granules are more affordable than virgin plastic granules while maintaining comparable quality for many applications. This cost advantage is crucial for industries looking to reduce production expenses without compromising on performance.
- They help manufacturers save on raw material costs.
- Lower production costs make recycled granules attractive for industries such as packaging, construction, and agriculture.
3. Applications in Green Industries
Recycled granules are at the forefront of green manufacturing practices. They are used in industries that prioritize sustainability, such as:
- Eco-friendly packaging: Bags, wraps, and containers made from recycled materials.
- Green construction materials: Pipes, panels, and insulation products.
- Sustainable agriculture: Irrigation pipes, seed trays, and greenhouse films.
Recycled plastic granules not only address environmental concerns but also provide industries with an economical and practical alternative to virgin plastics, making them an essential component of sustainable manufacturing.
How to Choose the Right Plastic Granules for Your Business
Selecting the right plastic granules is crucial for ensuring product quality, cost efficiency, and sustainability in your business operations. Here’s what to consider:
1. Factors to Consider
- Type of Granules: Determine whether you need virgin, recycled, or specialty granules based on your product requirements. For instance:
- Use LDPE Granules for flexible packaging and films.
- Opt for HDPE Granules for rigid and durable items like containers and pipes.
- Choose PP Granules for lightweight and heat-resistant products.
- Quality: Ensure the granules meet industry standards and are free from impurities. High-quality granules reduce defects in production and improve product durability.
- Supplier Reputation: Partner with suppliers known for reliability, consistent quality, and timely delivery. Look for certifications and customer reviews to validate their credibility.
2. Importance of Working with Reliable Suppliers
A dependable supplier ensures:
- Consistent quality, which is essential for maintaining your product standards.
- Access to diverse granule types tailored to your industry needs.
- Expert guidance in selecting the right granules for specific applications.
Working with a trusted Granules Manufacturer in Ahmedabad or a reputable Plastic Granules Manufacturer in India ensures your business remains competitive while meeting sustainability goals.
Future of Plastic Granules
The plastic granules industry is evolving rapidly, driven by technological advancements and the global push for sustainability. Here’s what the future holds:
1. Innovations in Granule Manufacturing
- Advanced Recycling Technologies: Enhanced methods like chemical recycling are improving the quality of recycled granules, making them comparable to virgin granules.
- Smart Granules: Incorporating features like biodegradability, UV resistance, and antimicrobial properties for specialized applications.
- Energy-Efficient Production: Innovations in machinery are reducing energy consumption, lowering the carbon footprint of granule production.
2. Trends in Sustainable Plastic Production
- Increased Use of Recycled Granules: Growing demand for eco-friendly alternatives in industries like packaging, construction, and consumer goods.
- Biodegradable Plastic Granules: Development of granules from plant-based polymers to reduce reliance on petrochemicals.
- Circular Economy Practices: Greater emphasis on closed-loop systems where plastic waste is continuously recycled into new granules.
With these advancements, plastic granules are poised to play a pivotal role in shaping a sustainable and innovative future for the plastic industry.
Conclusion
Plastic granules are the backbone of modern plastic manufacturing, providing industries with versatile, cost-effective, and scalable solutions. Whether it’s the flexibility of LDPE granules, the durability of HDPE granules, or the adaptability of PP granules, these tiny pellets are essential for creating a wide range of products used in everyday life.
Their significance extends beyond manufacturing; they are key players in the global push for sustainability. Recycled plastic granules, in particular, help reduce waste, conserve resources, and support eco-friendly practices, making them an invaluable resource in achieving a circular economy.
For businesses, choosing the right plastic granules and partnering with reliable suppliers ensures not only product quality but also a commitment to sustainable practices.
As the industry evolves, innovations and trends in sustainable production will continue to redefine the role of plastic granules, making them even more critical in building a greener and more efficient future. Understanding their importance today paves the way for more informed decisions that benefit businesses and the environment alike.